Why Heavy Copper PCB can improve the reliability of electronic equipment?
21 January 2025
Views: 1033
As the quest for improved performance, efficiency, and longevity of electronic devices continues, new technologies and materials are constantly being developed. In this regard, heavy copper PCBs have gained widespread recognition for their exceptional durability, enhanced current carrying capacity, and superior thermal management capabilities. By featuring copper layers thicker than those found in standard PCBs, heavy copper PCBs have opened up new possibilities in industries such as power electronics, automotive, aerospace, and renewable energy.
What are Heavy Copper PCBs?
Heavy copper PCBs, also known as thick copper or power copper PCBs, are circuit boards with copper layers that exceed the thickness of traditional PCBs. Manufacturing heavy copper PCBs is a more complex process than producing standard PCBs, as it involves specialized electroplating and etching techniques to ensure the desired copper weight on the finished board meets the required specifications.
While standard PCBs typically feature copper layers ranging from 1 to 3 ounces per square foot (oz/ft²), heavy copper PCBs can go beyond 4 oz/ft², reaching up to 20 oz/ft² or more. Compared to thinner copper layers found in standard PCBs, the increased copper thickness in heavy copper PCBs enables higher current capacity and improved heat dissipation.
Advantages of Heavy Copper PCBs
Enhanced Current Carrying Capacity:Heavy copper PCBs offer significantly higher current density compared to standard PCBs. This reduces the risk of overheating and voltage drop. Heavy copper PCBs are capable of handling much higher current levels, making them an ideal choice for high-power electronic applications such as motor drives, power supplies, and industrial equipment.
Improved Thermal Management:The increased copper mass in heavy copper PCBs acts as an efficient heat sink, allowing for better heat dissipation. This property enables effective spreading and dissipation of heat generated by high-power components such as processors, power regulators, and amplifiers. Heavy copper PCBs excel in high-power applications like LED lighting, automotive electronics, servers, telecommunications equipment, industrial control systems, and motor drives.
Enhanced Mechanical Strength:Heavy copper PCBs exhibit exceptional mechanical strength and durability. The increased copper thickness enhances the structural integrity of the boards, making them highly resistant to thermal stress, mechanical vibrations, and environmental factors. These attributes contribute to the longevity and reliability of heavy copper PCBs, making them suitable for demanding conditions encountered in the aerospace, military, and industrial sectors.
Simplified Design:Heavy copper PCBs allow for the integration of complex connections, such as high-speed signals, into simpler designs. Simplified designs can result in cost savings in production, assembly, and quality control processes.
Applications of Heavy Copper PCBs
Heavy copper PCBs are increasingly being utilized in a wide range of applications, particularly those requiring high power distribution and efficient heat dissipation. These applications include:
Automotive: Heavy copper PCBs are used in electric vehicles (EVs) and hybrid electric vehicles (HEVs) to support high-power battery management systems, motor controllers, and charging infrastructure. Their robustness and thermal management capabilities make them an excellent choice for automotive electronics.
Power Electronics: Heavy copper PCBs find extensive use in power electronic devices, including motor drives, inverters, converters, and high-current power supplies. The ability of heavy copper PCBs to handle high currents and dissipate heat efficiently ensures reliable operation in demanding power applications.
Renewable Energy: Heavy copper PCBs enable efficient power distribution and heat management, making them suitable for solar inverters, wind turbines, and energy storage systems. They facilitate high-efficiency power conversion, withstand high currents, and effectively manage heat dissipation.
Aerospace and Defense: Heavy copper PCBs' durability and thermal management characteristics make them suitable for the challenging conditions encountered in the aerospace and defense sectors. They are used in avionics, radar systems, communication equipment, and power distribution units.
Industrial Applications: Heavy copper PCBs, known for their reliability and longevity, are well-suited for various industrial equipment, including robotics, industrial control systems, and high-current connectors. They are also utilized in high-reliability sectors such as medical devices.
Conclusion
Heavy copper PCBs have emerged as an exceptional solution for applications demanding high current handling, efficient heat dissipation, and robustness. Their enhanced current carrying capacity, improved thermal management, and durability make them invaluable in power electronics, automotive, renewable energy, aerospace, and other high-reliability sectors. With their unmatched potential, heavy copper PCBs continue to revolutionize the electronics industry, enabling the development of innovative and reliable electronic systems across a wide range of industries.
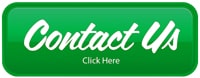