What is the role of solder mask in PCB manufacturing?
21 January 2025
Views: 577
The role of solder mask in PCB manufacturing
1. Solder protection: Leave the through holes and PAD on the board to be soldered, and cover all lines and copper surfaces to prevent short circuits during plug-in and save the amount of solder.
2. Protective board: Prevent moisture and other electrolytes from oxidizing the circuit and endangering electrical properties, and prevent external mechanical damage to maintain good insulation on the board.
3. Insulation: As the board becomes thinner and the line width and spacing become smaller and smaller, the insulation problem between conductors cannot be solved, which also increases the importance of the insulating properties of solder resist.
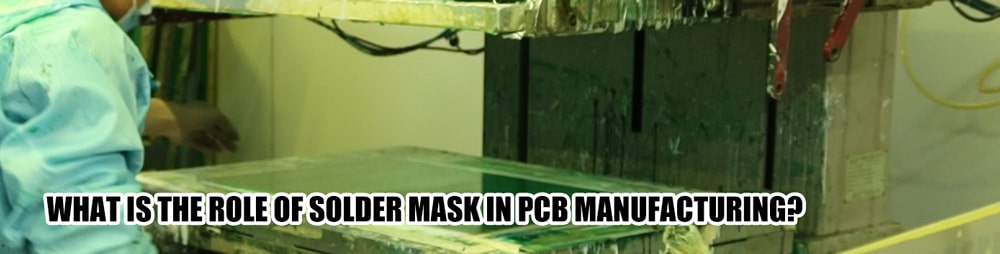
Why is solder mask green?
The solder resist paint was initially inspected by the staff, so more green pigment was added to the main paint. In addition to green, solder mask paint also comes in yellow, white, black and other colors. The types of solder mask include traditional epoxy resin IR baking type, UV curing type, liquid photosensitive ink, and dry film solder mask type, which are currently used Most of them are liquid photosensitive types.
Brief process of soldering mask
1. Pre-treatment; 2. Hole plugging; 3. Printing; 4. Pre-baking; 5. Exposure; 6. Development; 7. Post-baking.
In PCB manufacturing, solder mask is used to color the PCB and play the role of solder mask, insulation, and protection.
Share This Story, Choose Your Platform!