What is the role of nitrogen in PCB manufacturing?
21 January 2025
Views: 1258
The process of manufacturing and assembling printed circuit boards is complex. To ensure the best quality and reliability of PCBs, nitrogen is used in the PCB manufacturing process. But why is nitrogen used, and how does it affect the quality of PCBs? Let's find the answers to these questions in this article.
Why is nitrogen used?
By using nitrogen during PCB manufacturing, several benefits can be achieved, including protecting metal surfaces, controlling moisture, preventing contamination, and providing better temperature environments.
How does nitrogen affect the quality of PCBs?
During the manufacturing process of PCBs, oxygen is produced, and the residual oxygen can lead to oxidation of copper traces. This oxidation can damage the adhesion and conductivity of the plating, significantly reducing the product's lifespan. By replacing oxygen with nitrogen and creating an inert atmosphere, the copper surfaces are protected during critical steps such as etching, plating, soldering, and curing. This results in more durable PCB products with fewer issues, ultimately leading to higher quality.
What role does nitrogen play in the PCB manufacturing process?
1.Oxidation prevention: One of the key roles of nitrogen in PCB manufacturing is preventing oxidation during soldering and assembly processes. Nitrogen helps create an inert atmosphere, minimizing the contact of sensitive components with oxygen. By reducing the oxygen content, nitrogen effectively prevents the formation of an oxide layer on metal surfaces, ensuring clean and reliable solder joints. Industry standards require oxygen levels to be below 500ppm to avoid defects. Without nitrogen, oxidation issues would be prevalent, significantly reducing the yield. Plating tanks also operate optimally under a nitrogen layer, which helps control temperature fluctuations and bubble formation.
2.Miniaturization: With advancing technology, features like microvias and high-density interconnects require optimized nitrogen flow to displace gas voids during plating. Nitrogen flows into drilled holes and confined spaces, ensuring complete copper and solder coating inside small vias. For structures with blind vias and buried vias, nitrogen pressure and flow must be precisely calibrated. Without proper control, incomplete plating may occur, affecting electrical performance or causing delamination issues.
3.Automated assembly: In wave soldering and reflow ovens, inert nitrogen gas is used to swiftly transport circuit boards through the heating zone. Generally, 99.99% purity nitrogen ensures high-quality soldering. Nitrogen's thermal transfer properties enable full reflow soldering at high temperatures without causing thermal damage. It also protects sensitive components and solder paste from oxygen exposure during the assembly process. Transitioning to fully automated processes would be much more challenging without nitrogen as the carrier gas. Tighter process control can result in higher yields and more consistent joint quality.
4.Maximizing reliability: By eliminating oxidation issues throughout the entire manufacturing and assembly process, nitrogen helps reduce long-term reliability risks of PCBs. Without it, oxidation could compromise joint integrity or cause component degradation over time.
By incorporating nitrogen into the PCB manufacturing process, welding processes are enhanced, defects are reduced, oxidation and contamination are prevented, and the long-term reliability of assembled circuit boards is ensured. However, not all PCB suppliers utilize nitrogen. Choosing us, POE, will guarantee you the best PCB products with peace of mind.
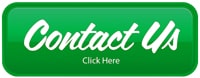
Email: all@poe-pcba.com
Share This Story, Choose Your Platform!