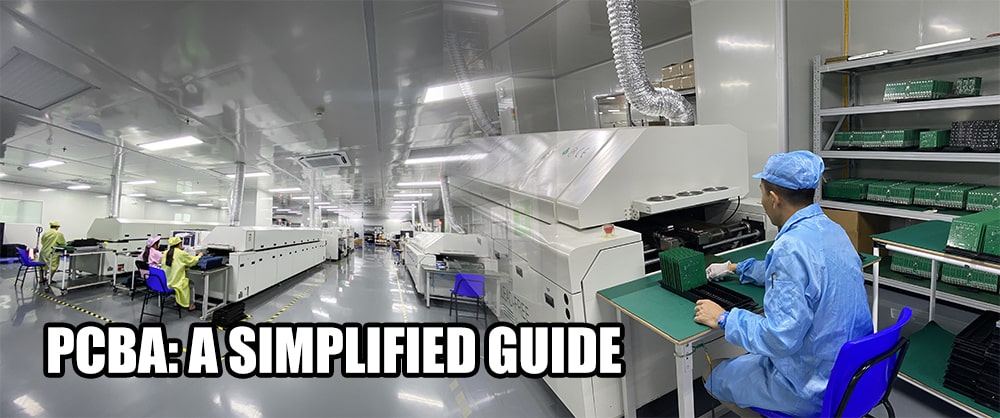
What is PCBA?
PCBA stands for Printed Circuit Board Assembly, which refers to the process of assembling electronic components onto a Printed Circuit Board to create a functional circuit. The components include integrated circuits (ICs), resistors, capacitors, diodes, and various other electrical and electronic devices.
Why is PCBA needed?
Printed Circuit Board Assembly is a critical stage in the electronics field where bare PCBs are transformed into operational devices capable of managing various electronic functions according to their design. It is essential for the operation of everyday devices such as smartphones, laptops, electronic systems in automobiles, and medical equipment, among others.
Basic Process of PCBA
Component Procurement
All necessary electronic components, such as integrated circuits (ICs), resistors, capacitors, connectors, etc., are procured based on the schematic diagram and bill of materials (BOM) provided by the customer. After receiving the components, we conduct inspections to ensure the quality of the components.
Preparation of Bare PCB
Prepare the bare PCB, which is in an unassembled state, with only copper traces and solder pads. Then, use an automated PCB assembly machine to prepare for the next steps.
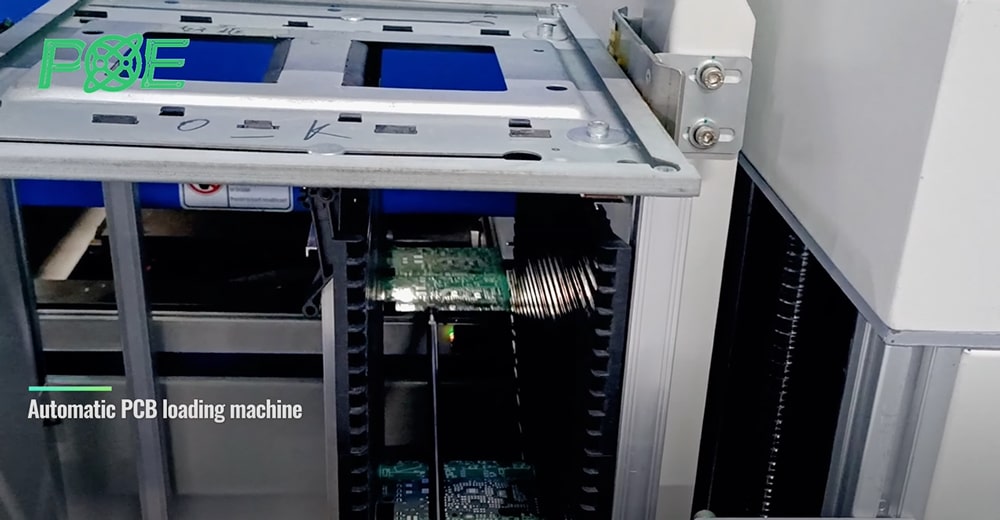
Solder Paste
The first step in PCBA is to apply solder paste to the areas of the circuit board where the components will be placed using an Automatic Solder Paste Printing Machine.
Component Placement(1)
Surface Mount Devices (SMD) or through-hole components are automatically placed on the PCB using a pick-and-place machine according to their designations. Some components may require manual placement.
Component Placement(2)If through-hole assembly is used, then this is the process. Through-hole assembly is typically employed for larger, heavier components or those requiring additional mechanical strength to enhance their connection with the PCB. The process involves Through-Hole Components Lead Forming, Insertion of Through-Hole Components, and Wave Soldering in the Oven.
QC before Oven
Before sending the PCB into the reflow oven for soldering, we conduct quality control to inspect the components and solder paste on the PCB, ensuring that everything meets the required standards.
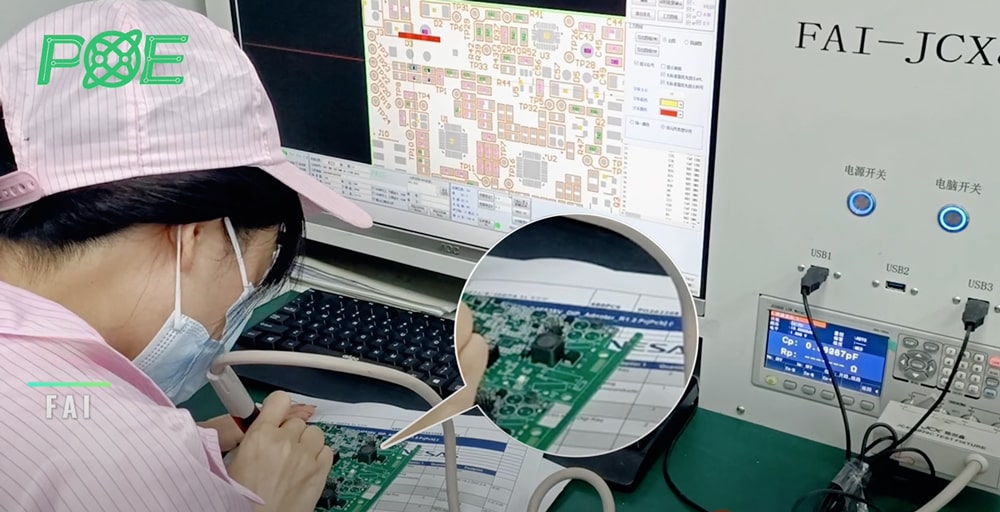
Reflow Soldering
The PCB is passed through an oven or reflow chamber, where the components are soldered onto the pads using the reflow soldering process. This ensures electrical connections between all the components and nitrogen gas is often used to remove excess oxygen, enhancing product reliability.
Testing
Prototype testing, functional testing, environmental testing, reliability testing, in-circuit testing, basic functional testing, automated optical inspection (AOI), X-ray testing, RoHS testing, and other tests are conducted to ensure accurate component placement and soldering according to design specifications, ensuring product quality.
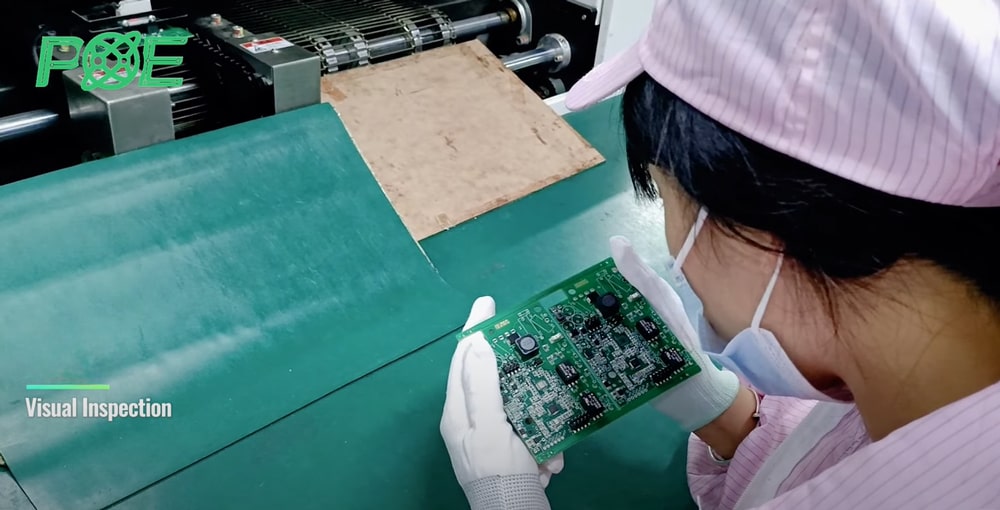
Quality Control
Final inspections are carried out to ensure shape, fit, and functionality meet the design requirements before shipping or further assembly.
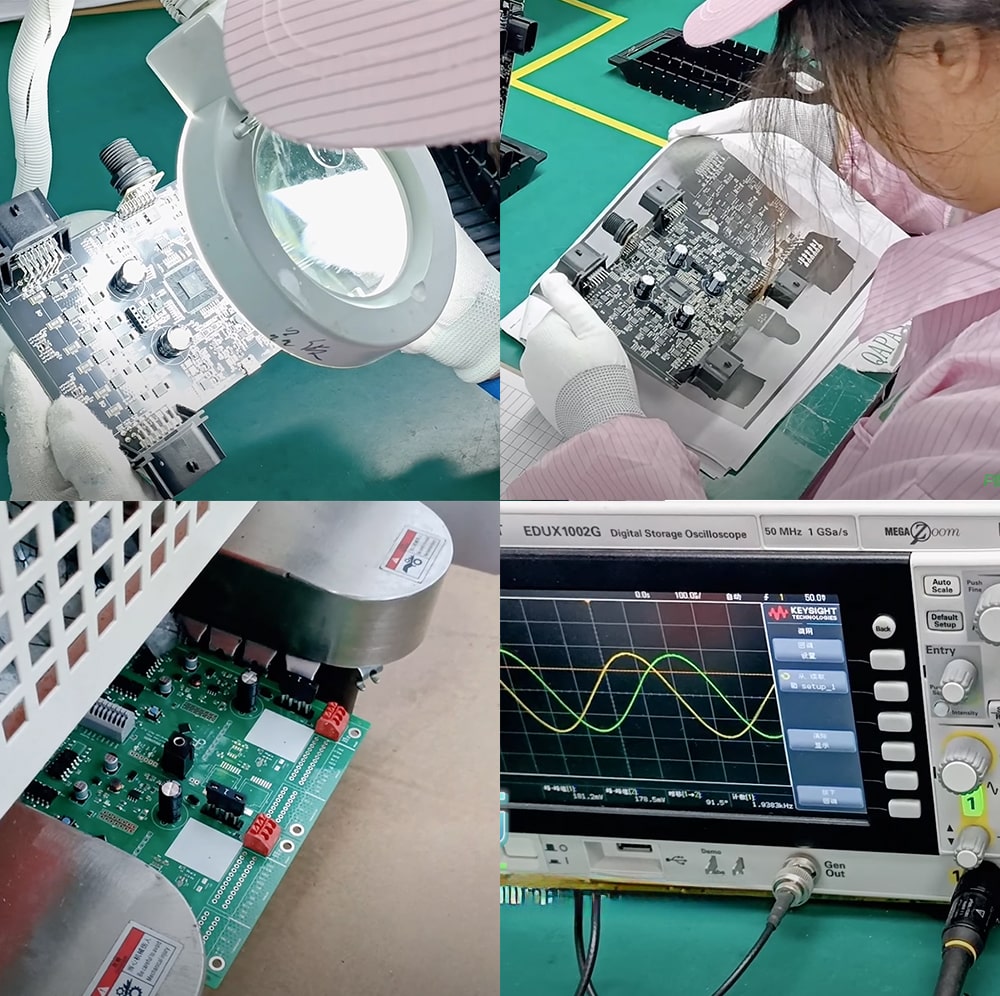
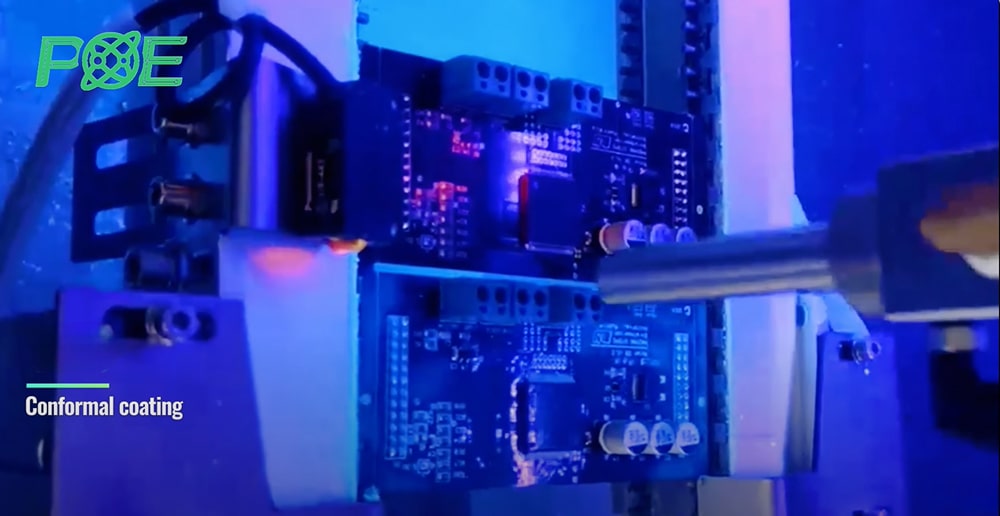
Packaging
Completed PCBA is packaged using anti-static materials and transported to the customers.
PCBA, with its efficiency and compactness, finds wide applications in various industries, ranging from consumer electronics like smartphones and televisions to industrial machinery control and automotive systems. It is an integral part of today's technology-driven world. If you have any PCBA requirements, feel free to contact us. We, at POE, have over 20 years of experience in PCB manufacturing and assembly, guaranteeing 100% reliable products for our customers!
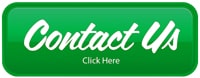
Email: all@poe-pcba.com