PCB DFM: Achieving Efficiency and Reliability Key
21 January 2025
Views: 1169
In complex electronic devices, the Printed Circuit Board is a core component that carries the electrical functionality of the device. Therefore, ensuring excellent PCB design is crucial for the final quality and performance of the product, and Design for Manufacturing (DFM) is the best tool to address this challenge.
What is PCB DFM?
DFM (Design for Manufacturing) is a design concept that encompasses the entire process from initial design to final assembly, including aspects such as material selection, layer design, layout, routing, and manufacturing details. This design approach helps engineers create products that are easier to manufacture, more reliable, and cost-effective. By implementing DFM, it is possible to reduce product iterations, lower waste and scrap rates, improve production efficiency, and ultimately reduce product costs while enhancing product quality.
Why is DFM so important for PCB design?
Improved production efficiency: Optimizing the design through DFM enables rational component layout and simplification of the assembly process, reducing production time and significantly enhancing production efficiency.
Cost reduction: DFM can lower overall manufacturing costs by minimizing errors and rework during the manufacturing process.
Ensuring quality: Adhering to DFM specifications ensures manufacturing quality and reliability of PCBs, thereby enhancing the overall product performance.
Implementation process of PCB DFM
1.Understanding the manufacturing process: Gain knowledge of every step involved in the manufacturing process, from material selection to drilling, plating, and circuitry, to anticipate potential issues during the design phase.
2.Design for manufacturability rule check: Conduct self-checks against manufacturing rules and standards in the early stages of design to ensure manufacturability.
3.Design review: Perform internal or external design reviews at different stages of the design to promptly identify and address potential design issues.
4.Prototype testing: Test the design by creating prototypes between the design and manufacturing stages to identify and resolve potential problems before actual production.
5.Feedback and improvement: Provide feedback to the designer on any issues encountered during the manufacturing process to facilitate improvement and optimization.
Four ways to improve PCB DFM quality
1.Strengthen design specifications: Clearly define design specifications and ensure designers understand and comply with these standards.
2.Optimize layout: Optimize component placement for easy identification and installation, reducing the need for expensive or vulnerable process steps. Well-designed layout can significantly improve PCB manufacturability.
3.Select appropriate materials: Choose materials that are suitable for the manufacturing process and product requirements.
4.Introduce automation: Automated Optical Inspection (AOI) equipment can provide real-time PCB inspection during the production process, reducing human errors and improving production efficiency.
Summary
PCB DFM is a critical design process that contributes to ensuring manufacturability, improving product quality, reducing costs, and shortening time to market. If you require DFM services and prototype manufacturing for your PCB products, please feel free to contact us.
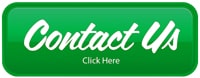