How to do SMT factory ESD protection?
21 January 2025
Views: 72
What is SMT Factory ESD?ESD in SMT factories refers to the phenomenon that static electricity is transferred from one charged object to another. Electronic components are very sensitive to static electricity, especially ICs, chips, etc. If ESD is not properly managed, it may cause component damage.
How to do SMT factory ESD protection?In order to ensure that SMT factories do not have product quality problems caused by static electricity, common ESD protection measures are as follows:
1. Establish an ESD Protection Area (EPA)
The EPA (electrostatic protection area) is a specially designated area within the SMT factory where all ESD sensitive devices are processed and stored. Personnel and tools entering this area must be treated with anti-static treatment.
2. ESD protection equipment
Anti-static workbench: Use anti-static materials to cover the workbench to prevent static electricity accumulation.
Grounding system: All workbenches, equipment and tools should be grounded so that static electricity can be safely released through the grounding system.
Anti-static packaging: Use special packaging materials such as anti-static bags and anti-static trays to protect devices from static electricity.
3. Personnel protection
Wear anti-static clothing: Workers need to wear anti-static work clothes, anti-static shoes, and anti-static wrist straps when working.
Grounding wrist straps: Employees need to wear grounding wrist straps to release body static electricity through the grounding wire to prevent static electricity from being transferred to sensitive components.
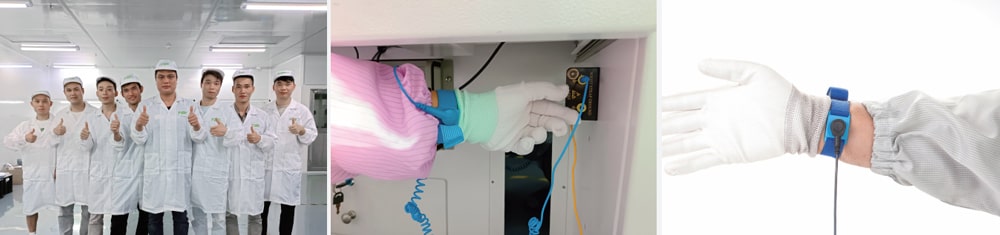
4. Environmental control
Humidity control: A dry environment is prone to static electricity accumulation. It is generally recommended to keep the relative humidity between 40%-60% to reduce the generation of static electricity
5. ESD monitoring and detection
Use static voltage detectors, wristband monitors, surface resistance testers and other equipment to monitor and measure the static electricity level in the factory environment in real time to ensure that static electricity remains within a safe range.
6. ESD training
Employees need to receive regular ESD protection knowledge training to understand how to prevent static electricity and how to properly handle ESD sensitive components.
What is a qualified SMT factory ESD?
A qualified SMT factory ESD management. The system needs to meet the following standards:
1. Follow international standards
The factory should follow international electrostatic protection standards such as IEC 61340-5-1 (static control standard) or ANSI/ESD S20.20 (electrostatic discharge control standard), which define how to effectively manage and control static electricity.
2. EPA area setting compliance
A qualified SMT factory must have a clear ESD protection area (EPA), and all equipment, tools and personnel in the EPA area must follow strict anti-static specifications.
3. Effective ESD protection equipment
The factory should be equipped with qualified anti-static equipment and ensure that these equipment are in normal working condition. Including grounding system, anti-static workbench, anti-static tools, etc.
4. Continuous monitoring and recording
Monitor the real-time static level of the electrostatic protection area and keep records for review. Regularly check the effectiveness of wrist straps and grounding systems.
5. Regular maintenance and audit
ESD protection systems need to be regularly maintained and updated to ensure compliance with the latest anti-static standards. In addition, regular third-party or internal ESD audits are also key to ensuring the effectiveness of the protection system.
6. Personnel training and compliance
Factory personnel should have sufficient ESD knowledge and receive regular retraining to ensure that they can effectively implement the factory's ESD management system.
Conclusion: ESD protection in SMT factories is a key link in ensuring the quality of electronic components and finished products. By establishing electrostatic protection areas, using anti-static equipment and tools, managing environmental humidity, training personnel, and following international standards, qualified SMT factories can effectively reduce the impact of ESD on product quality.