DFA vs DFM: What's the Difference and Why Does It Matter?
21 January 2025
Views: 3668
Design for Assembly (DFA) and Design for Manufacturability (DFM) are two important concepts in PCB design of printed circuit boards. Both DFA and DFM aim to optimize the PCB design process to improve production efficiency and reduce costs. In this article, we will explore the difference between DFA and DFM and their importance in PCB design.
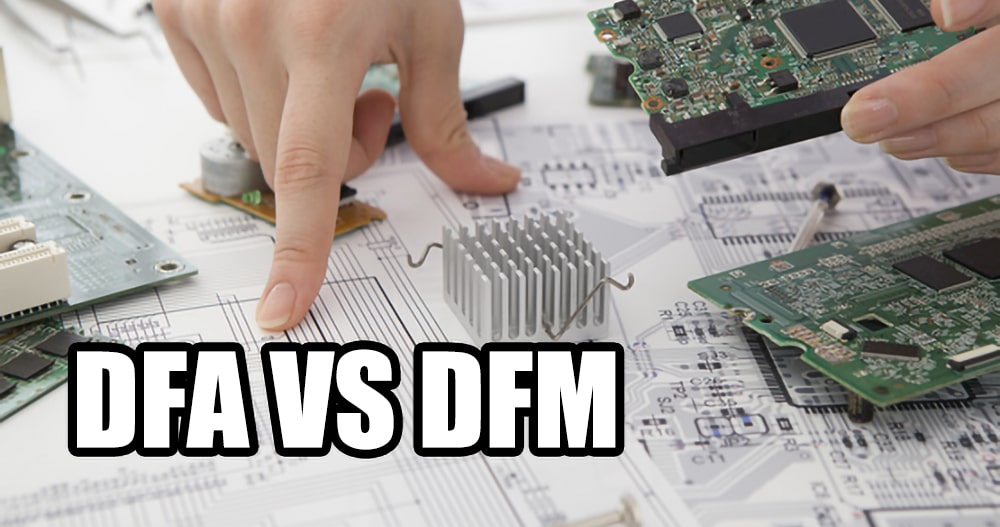
What are DFA?
Design for Assembly (DFA) is a design methodology that focuses on optimizing PCB designs to make PCB products easier and more efficient to assemble. The main goal of DFA is to reduce the number of assembly steps and the time required for each step, which can significantly reduce the overall assembly time and cost.
DFA considers the assembly process when designing a PCB, including the selection of components and their placement on the board, minimizing the number of assembly steps required. For example, if two components need to be soldered together, they should be placed as close together as possible to reduce the time and effort required for the soldering process.
DFA also designs the board with the assembly process in mind, designs the board to be easy to handle, and provides clear instructions for the assembly process. For example, circuit boards should be designed with clear markings to indicate the orientation and assembly sequence of components.
What are DFM?
Design for Manufacturability (DFM) is a design methodology that focuses on optimizing PCB design to make PCB manufacturing easier and more cost-effective. The main goal of DFM is to reduce the number of PCB manufacturing defects and improve the yield of the manufacturing process.
DFM can take into account the manufacturing process, including selecting the most suitable materials and manufacturing processes for the design. For example, if the design includes components that require a specific manufacturing process, such as surface mount technology (SMT), the board should be designed to be compatible with that process.
DFM also takes into account designing boards with proper tolerances and clearances to ensure a successful manufacturing process. For example, circuit boards should be designed with proper spacing between components to avoid short circuits or other manufacturing defects.
What's the difference between DFA and DFM?
DFA and DFM are related, but they have different main goals, focusing on different aspects of PCB design. The key difference between DFA and DFM is that DFA focuses on optimizing the assembly process whereas DFM focuses on optimizing the manufacturing process.
The main purpose of DFA is to reduce the number of assembly steps and the time required for each step. This includes selecting components and their placement during assembly to minimize the number of assembly steps required, and designing the board for ease of handling and assembly.
The main purpose of DFM is to reduce the number of manufacturing defects and increase the yield of the manufacturing process. Designing boards with the manufacturing process in mind, selecting materials and manufacturing processes that are best suited for the design, and designing boards with proper tolerances and clearances to ensure a successful manufacturing process.
To implement DFA and DFM in your PCB design process, you should follow some best practices:
1.Involve your PCB manufacturing partner in the design: Involve your PCB manufacturing partner in the design as early as possible, which will help ensure that the manufacturing process of your PCB design PCB factory is compatible, and detect and solve any potential problems as early as possible.
2.Use of standard components: Using standard components helps to reduce the number of assembly steps required and increase the yield of the manufacturing process. Standard components are available everywhere and are designed to be compatible with various manufacturing processes.
3.Optimizing component placement: Optimizing component placement helps reduce the number of assembly steps required. Components should be placed close together to reduce the time and effort required for the assembly process.
4.Design for Testability: Design for Testability helps in reducing the number of manufacturing defects. The board should be designed with test points and access points for easy testing and debugging.
Conclusion
Design for Assemblability (DFA) and Design for Manufacturability (DFM) are two important concepts in PCB design that focus on optimizing the design process to increase production efficiency and reduce costs. DFA focuses on optimizing the assembly process while DFM focuses on optimizing the manufacturing process. Getting your manufacturing partner involved in your PCB design as early as possible helps to help the project go online faster. POE has more than 20 years of rich experience in PCB manufacturing. Contact us to start your project immediately!
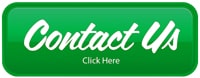
Share This Story, Choose Your Platform!