POE manufacturing,your global technology partner. POE has been working with many customers from Europe and USA who need airplane and space PCB/PCBAs. Our sourcing team is always excited to introduce any negative and positive components for your design. We hope mutual support and help to reach a mutual-profit products with our customers.
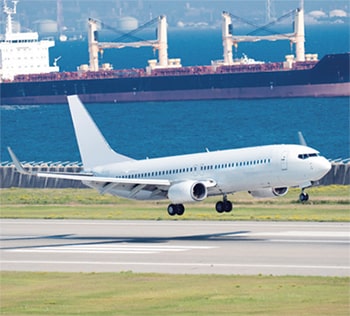
For example, Microchip introduced a series of configurable driving boards, using hybrid power driving modules based on silicon carbide (SiC) or silicon (Si) technology. Driven by the important goal of sustainable development and emission reduction, the aviation industry needs advanced, efficient and low-emissio aircraft.
In order to achieve these goals, aviation power system developers are transforming to electric actuation systems, which will promote the vigorous development of multi-electric aircraft (MEA). In order to provide a comprehensive electric actuation solution for the aviation industry, Microchip Technology Inc today announced the launch of a new integrated actuation power supply solution. The new solution combines the matched grid driver board with our extended hybrid drive (HPD) module with silicon carbide ord silicon technology, and the power range is 5 kVA to 20 kVA. Regardless ofd the power output, the new integrated actuating power supply solution can maintain the same substrate surface.
In order to achieve these goals, aviation power system developers are transforming to electric actuation systems, which will promote the vigorous development of multi-electric aircraft (MEA). In order to provide a comprehensive electric actuation solution for the aviation industry, Microchip Technology Inc today announced the launch of a new integrated actuation power supply solution. The new solution combines the matched grid driver board with our extended hybrid drive (HPD) module with silicon carbide or silicon technology, and the power range is 5 kVA to 20 kVA. Regardless of the power output, the new integrated actuating power supply solution can maintain the same substrate surface.
The grid drive board can be integrated with the HPD module of Microchip, providing an integrated motor drive solution for the electrification of flight control, braking and landing gear systems. Microchip's power supply solutions can be expanded according to the requirements of the final application, from small actuation systems for unmanned aerial vehicles to high-power actuation systems for electric vertical takeoff and landing (eVTOL) aircraft, MEA and all-electric aircraft. Leon Gross, vice president in charge of discrete products department of Microchip, said: "The grid driver board we developed can be used together with our existing HPD module to provide plug-and-play MEA power supply solutions for the market. With this solution, customers no longer need to design and develop their own driving circuits, thus reducing design time, resources and costs."
The test conditions of these high-reliability devices conform to DO-160 "Environmental Conditions and Test Procedures for Airborne Equipment", and they have various protection functions, including breakdown detection, short-circuit protection, unsaturated protection, under-voltage locking (UVLO) and active miller clamping. The gate drive circuit board is driven by external PWM signal based on low voltage differential signal (LVDS) conforming to TIA/EIA-644 standard, which has low electromagnetic interference (EMI) and good anti-noise ability.
The grid driving board provides differential output for telemetry signals such as DC bus current, phase current and solenoid valve current by obtaining feedback from shunt and DC bus voltage in HPD module. It also provides direct output for two PT1000 temperature sensors in HPD power supply module. The supporting grid drive board is a compact solution with light weight and small shape, which can optimize the size and energy efficiency of the actuating system.
The working temperature range of the gate driver is-55 C to+110 C, which is very important for aviation applications that are often exposed to harsh environments. The isolated gate driving board only needs 15V DC input for controlling and driving the circuit. All other voltages required are generated on the board. This greatly reduces the number of system components and simplifies the system wiring.
And UAV products is also within our manufacturing capability.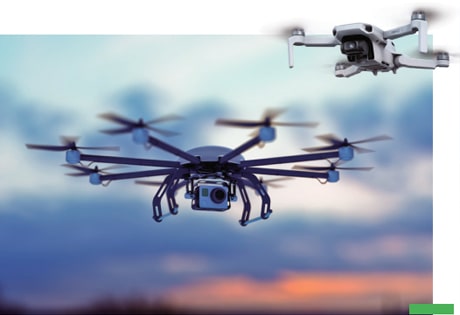
Highlights of UAV system solutions as an aerial robot, UAV can be used for reconnaissance, surveillance, etc.. In military, geodesy, shaking sensation, etc.. In civil, it mainly hopes to obtain two-dimensional or three-dimensional images with high resolution, but the amount of high-resolution image data is quite large, and with the improvement of ground resolution, the amount of image data to be transmitted increases geometrically, and the data code rate also increases rapidly. Therefore, the high-speed transmission of images has become an important problem that restricts the application of UAV.