Aerospace PCB Manufacturing & Assembly
21 January 2025
Views: 2697
The aerospace industry demands excellence in reliability, performance, and safety. At the core of these stringent requirements is the need for high-quality PCB assembly to ensure seamless operation in aerospace applications. So, how can high-quality aerospace PCB assembly be achieved, and how can collaboration with the right PCB assembly supplier propel aerospace projects to new heights?
Aerospace PCB Assembly Standards and Requirements
Aerospace PCB assembly necessitates strict specifications and requirements to ensure its reliability, durability, and safety. The following key specifications and requirements must be met during the PCB assembly process for aerospace applications:
AS9100: This aerospace-specific Quality Management System (QMS) standard covers the entire manufacturing process, including PCB assembly.
IPC-A-610: IPC-A-610 is widely regarded as the standard for accepting assembled electronic products, defining acceptable process standards for electronic component assembly.
ISO 9001: This internationally recognized QMS focuses on consistency and customer satisfaction.
Component Sourcing: Aerospace components should be sourced from reliable suppliers to minimize the risk of counterfeit and non-compliant parts. Traceability and tracking of materials must be maintained throughout the assembly process.
High-Reliability Components: Aerospace applications require the use of high-reliability components, such as Rad-Hard (radiation-resistant) and Hi-Rel (high-reliability) grade parts, capable of withstanding extreme conditions.
High-Precision Assembly: Aerospace PCB assembly necessitates precise component placement while adhering to strict alignment tolerances and solder joint quality. Effective soldering techniques, including wave soldering, selective soldering, and reflow soldering, should be employed based on component types and PCB design.
Conformal Coating: Applying protective conformal coatings to safeguard assembled PCBs from environmental factors such as moisture, dust, and extreme temperatures can enhance durability and reliability.
Inspection and Testing: Rigorous inspection and testing should be performed at various stages of the PCB assembly process to ensure adherence to design specifications and quality requirements. This includes Automatic Optical Inspection (AOI), X-ray inspection, In-Circuit Testing (ICT), functional testing, and Electrostatic Discharge (ESD) control.
Proper Documentation: Detailed documentation, including assembly drawings, Bills of Materials (BOM), and assembly instructions, is crucial for ensuring correct assembly and traceability.
Cleanliness and Safety: Aerospace PCB assembly requires high-standard cleanroom environments to minimize the risks of contamination and failures.
Aerospace PCB Material Selection
Choosing the appropriate PCB materials is crucial for high-quality aerospace PCB assembly. Some recommended materials include:
Polyimide: Polyimide-based PCBs, such as DuPont's Kapton or Arlon's 85N, are widely used for aerospace applications due to their excellent thermal stability, mechanical strength, and resistance to chemicals. Polyimide materials can operate effectively in a wide temperature range (-260°C to +400°C) and have low outgassing properties, making them suitable for space applications.
PTFE (Teflon): Polytetrafluoroethylene materials, such as Rogers' RT/duroid, Taconic's T-lam, or Arlon's CuClad series, exhibit low dielectric constant and low dissipation factors, allowing for high-frequency signal transmission. Their low moisture absorption, chemical resistance, and thermal stability make them suitable for aerospace applications.
LCP (Liquid Crystal Polymer): LCP materials, such as Rogers' ULTRALAM 3000 series, are suitable for high-temperature and high-frequency aerospace applications due to their low dielectric constant, low moisture absorption, and excellent dimensional stability. They also perform well in harsh environments such as space.
FR-4: FR-4, the most commonly used PCB material, can be used for specific aerospace applications where environmental conditions are less severe. High-quality FR-4 laminates with high glass transition temperatures and flame-retardant properties may still be suitable for selected aerospace applications.
Ceramic Substrates: For high-temperature and high-reliability aerospace applications, such as engine control modules, ceramic-based PCB substrates such as aluminum nitride (AlN) or aluminum oxide (Al2O3) may be used. These materials provide excellent thermal conductivity, mechanical strength, and electrical insulation properties.
The assembly of PCBs used in aerospace applications needs to be performed with the highest precision and reliability. Process Steps for Aerospace PCB Assembly Services Provided by POE: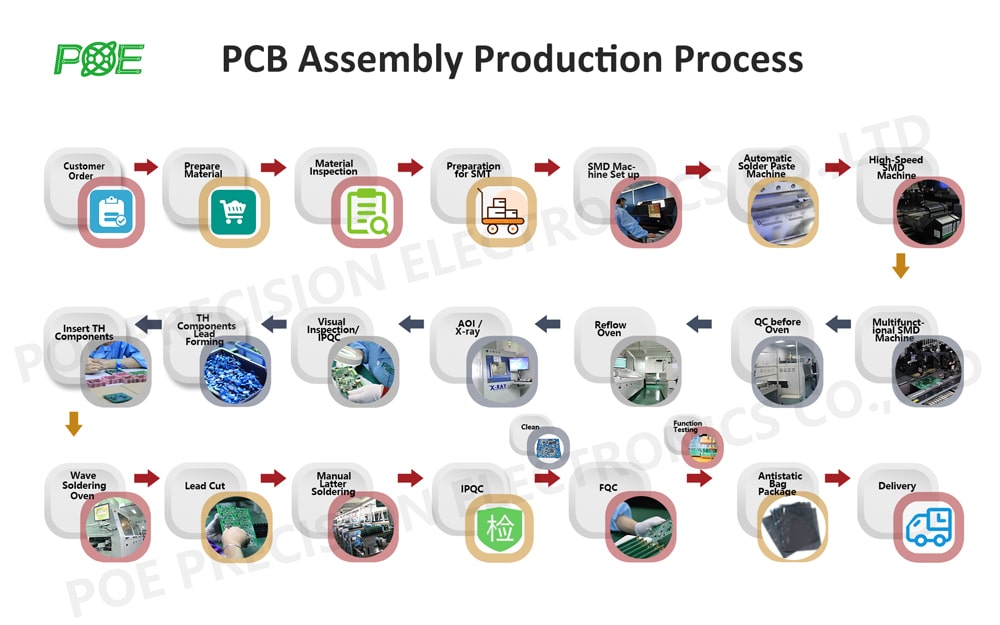
1.Design and Engineering: The first step involves designing the PCB layout, considering the specific requirements of aerospace applications. This includes selecting suitable PCB materials, optimizing component layout, signal routing, and thermal management. If you already have files, we can also provide PCB manufacturing and assembly services.
2.Material Procurement and Inspection: The next step involves purchasing the necessary PCB substrates and components for assembly. Ensure that all materials meet the quality and reliability requirements of aerospace applications.
3.PCB Fabrication: The selected PCB materials are fabricated according to the design specifications, involving processes such as etching, drilling, plating, and lamination.
4.Solder Paste Application: A thin layer of solder paste is applied to the PCB pads using a solder paste stencil. The solder paste acts as an adhesive, temporarily holding the components in place and forming a strong solder joint after reflow.
5.Component Placement: Electronic components are placed on the PCB using an automated pick-and-place machine or, for special components and assembly types, manual placement methods. This stage requires high precision to avoid misalignment of components.
6.Reflow Soldering: The components on the PCB are temporarily held in place with solder paste and then passed through a reflow oven. The solder paste is heated, forming a strong solder joint between the components and the PCB pads.
7.Inspection and Testing: To ensure that the assembled PCB meets the design specifications and quality requirements, it undergoes various inspection and testing procedures such as Automated Optical Inspection (AOI), X-ray inspection, In-Circuit Testing (ICT), or functional testing.
8.Rework and Repair: If any defects are found during the inspection and testing process, they need to be corrected through rework and repair. This may involve removing and replacing faulty components or addressing soldering issues.
9.Conformal Coating Application: A protective conformal coating is applied to the PCB components to protect them from environmental factors such as moisture, dust, and harsh temperatures. This enhances the durability and reliability of the PCB.
10.Final Assembly: The PCB components are installed in their final enclosure or housing and integrated with other components and systems.
11.Full System Testing: The overall performance of the system is tested to ensure that it meets the requirements of aerospace applications.
12.Documentation and Traceability: Detailed documentation is maintained throughout the assembly process, including assembly drawings, Bill of Materials (BOM), test results, and inspection records required for aerospace certification and traceability.
The aerospace PCB assembly process requires strict adherence to quality standards, high-precision manufacturing, thorough inspection and testing, and high-quality component selection and procurement. With over 20 years of experience in PCB manufacturing and assembly, you can trust POE to provide one-stop PCB manufacturing and assembly services.
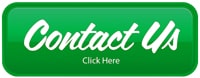
Why Choose POE as Your Aerospace PCB Supplier?
Expertise: We have extensive experience in the aerospace PCB assembly industry, with over 20 years of PCB manufacturing and assembly experience.
Advanced Technology: We use advanced PCB manufacturing, assembly, and testing technologies to provide high-quality, reliable, and durable products suitable for aerospace applications.
Comprehensive Services: From PCB manufacturing and engineering support to post-production assistance, we provide a full range of PCB assembly services to meet all aspects of the product lifecycle.
Custom Solutions: We take pride in understanding each customer's unique needs and developing custom solutions to meet their specific requirements, ensuring optimal performance and functionality.
High Quality Assurance: Our strict quality control processes and adherence to industry standards ensure that our aerospace PCB assemblies meet 100% high-quality, safety, and reliability requirements.
One-Stop Services: We provide open, transparent communication and assistance throughout the project lifecycle, addressing inquiries, providing updates, and fostering strong working relationships.
Competitive Pricing: We strive to provide cost-effective solutions while ensuring high-quality standards required for aerospace PCBs.
Choosing POE to meet your aerospace PCB assembly needs ensures that you have a reliable partner dedicated to providing 100% high-quality products and services.
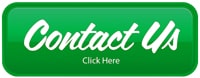